Machine Scheduling Software
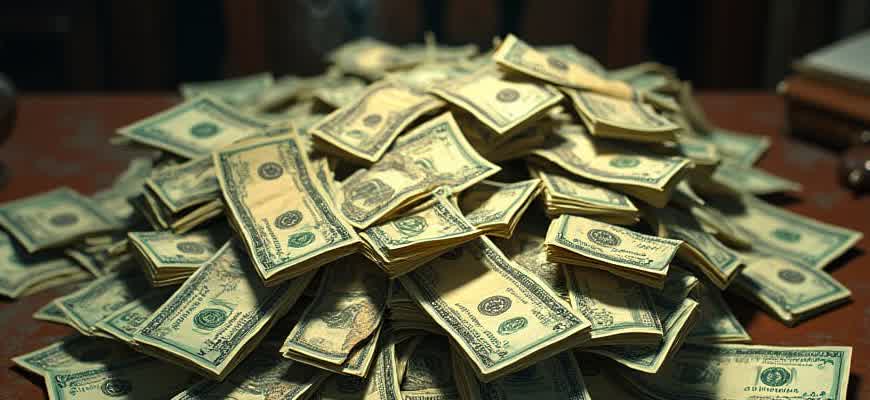
Machine scheduling systems are critical tools used in manufacturing and production environments to allocate resources, manage production time, and optimize workflow. These systems help plan, control, and track operations across various machinery, ensuring maximum efficiency and minimal downtime. A well-designed scheduling system is crucial for improving throughput and reducing operational costs by dynamically adjusting production schedules based on machine availability, job priorities, and resource constraints.
Key features of machine scheduling software typically include:
- Real-time scheduling and monitoring
- Automated job prioritization
- Resource allocation based on machine capabilities
- Integration with other production management tools
These features provide manufacturers with the ability to quickly respond to changing demands, maintain equipment reliability, and meet deadlines efficiently.
Fact: According to industry reports, companies using advanced machine scheduling software have reported a reduction in production lead time by up to 30%.
When selecting a machine scheduling solution, it's important to consider factors such as:
- Ease of integration with existing systems
- Scalability for future growth
- Support for multi-machine and multi-shift environments
- User-friendly interface for quick adoption
The effectiveness of a machine scheduling tool is greatly influenced by its adaptability to different production scenarios and its ability to handle complex scheduling tasks.
Feature | Benefit |
---|---|
Real-time Monitoring | Helps in tracking machine performance and uptime |
Automated Scheduling | Reduces human error and optimizes task distribution |
Resource Allocation | Ensures machines are utilized effectively, avoiding overwork or idle time |
Choosing the Right Machine Scheduling Tool for Your Business
When selecting a machine scheduling solution, businesses need to carefully assess their operational needs and how the software will integrate with existing systems. An ideal tool will streamline production workflows, enhance resource utilization, and minimize downtime. Each manufacturing environment has unique demands, so identifying a tool that fits your specific goals is crucial to maintaining efficiency and productivity.
Different scheduling software options offer a variety of features. From basic production planning to advanced machine learning integrations, it's essential to evaluate the scope of functionality required by your team. Consider the size of your operation, the complexity of your workflows, and the level of automation you desire when making your choice.
Key Considerations for Choosing a Scheduling Tool
- Ease of Integration: Ensure the tool can seamlessly connect with your existing ERP or other business systems.
- Real-time Data Updates: A tool that provides live data feeds can help in making informed decisions on the fly.
- Scalability: Consider whether the solution will grow with your business, accommodating new machines or processes.
- Customization: The ability to tailor the software to specific business processes can greatly enhance efficiency.
Important: The right scheduling software can significantly reduce operational bottlenecks and improve production scheduling accuracy, but choosing the wrong one can lead to inefficiencies and increased costs.
How to Evaluate Machine Scheduling Tools
- Assess Business Needs: Evaluate the type and scale of production, as well as key scheduling requirements.
- Request Demos and Trials: Test different tools in real-world scenarios to understand their capabilities.
- Check Customer Support: Reliable customer service is crucial for resolving issues and ensuring smooth software implementation.
Feature | Basic Tool | Advanced Tool |
---|---|---|
Real-Time Scheduling | Limited | Full Integration |
Mobile Access | No | Yes |
Customization Options | Minimal | Highly Customizable |
Cost | Low | High |
Maximizing Resource Utilization with Machine Scheduling Features
Effective machine scheduling is crucial for enhancing resource utilization in manufacturing environments. By leveraging advanced scheduling features, companies can optimize machine time, reduce downtime, and streamline operations. Key tools in scheduling software allow manufacturers to better allocate resources based on demand, maintenance schedules, and production priorities, ensuring that machines are running at their full potential.
Machine scheduling solutions are designed to dynamically adjust to shifting production requirements. With the right scheduling features, manufacturers can adapt to changes quickly, allocate resources more efficiently, and minimize wasted capacity. By prioritizing tasks based on urgency and machine availability, businesses can achieve better throughput and overall resource optimization.
Key Features for Maximizing Resource Utilization
- Real-time Monitoring: Tracks machine performance, identifying underutilized assets and potential bottlenecks in real-time.
- Automated Scheduling: Automatically assigns tasks to machines based on availability, reducing manual intervention and optimizing job completion times.
- Maintenance Integration: Schedules preventive maintenance in advance, preventing unexpected downtime and ensuring that machines are always in top condition.
"By continuously monitoring machine availability and performance, manufacturers can ensure maximum uptime and minimize costly delays."
Benefits of Effective Resource Allocation
- Reduced Idle Time: Minimizes periods when machines are not in use, leading to increased productivity.
- Improved Scheduling Accuracy: By factoring in real-time data, machine scheduling tools can create more precise production timelines.
- Enhanced Flexibility: The ability to quickly shift resources or reassign tasks ensures that production runs smoothly even in the face of unexpected challenges.
Resource Utilization in Practice
Machine | Availability | Utilization Rate | Scheduled Maintenance |
---|---|---|---|
Machine A | 98% | 95% | May 15 |
Machine B | 100% | 90% | June 1 |
Machine C | 92% | 88% | May 30 |
Reducing Downtime: Practical Ways to Leverage Scheduling Software
Machine downtime can significantly impact productivity and profits. By effectively utilizing scheduling software, companies can streamline operations, minimize idle time, and improve overall equipment efficiency. Proper scheduling ensures that machines are in use when needed, without unnecessary delays or overlap. With the right approach, businesses can drastically reduce the cost of unplanned downtime.
Implementing machine scheduling software provides a comprehensive solution for tracking and optimizing the use of machines across production lines. This software can help in planning maintenance, allocating resources, and tracking machine performance in real time. Below are some practical strategies for reducing downtime through effective scheduling:
Effective Scheduling Strategies
- Predictive Maintenance: Schedule maintenance activities based on usage and historical data to prevent sudden breakdowns.
- Real-Time Monitoring: Leverage the software to track machine status and performance, allowing immediate responses to emerging issues.
- Resource Optimization: Maximize machine utilization by aligning production schedules with available resources, reducing idle time.
Key Features of Scheduling Software
Feature | Benefit |
---|---|
Real-Time Alerts | Helps identify issues before they cause downtime. |
Automated Scheduling | Reduces human error and optimizes production flow. |
Data Analytics | Provides insights for continuous improvement and better resource management. |
"By integrating machine scheduling software, companies can ensure that preventive measures are taken before breakdowns occur, reducing costly downtime and enhancing operational efficiency."
Cost-Effective Implementation of Machine Scheduling in Manufacturing
Incorporating machine scheduling software into manufacturing operations can lead to substantial cost savings, but the process must be handled with strategic planning to maximize the return on investment. A well-designed scheduling system ensures optimal machine usage, reduces downtime, and enhances overall productivity. The key to cost-effective implementation lies in aligning the software’s capabilities with the specific needs of the production environment.
To implement machine scheduling effectively, manufacturers should focus on optimizing resource allocation, minimizing waste, and improving throughput. While many software solutions offer complex features, it’s essential to select a solution that delivers the necessary functionality without over-complicating the process or inflating costs.
Key Steps for a Cost-Effective Machine Scheduling Implementation
- Evaluate specific production needs: Understanding the unique challenges of the production floor ensures that the chosen scheduling software fits well with current operations.
- Integrate with existing systems: To reduce implementation costs, choose a system that can be easily integrated with current ERP, MES, or other relevant software.
- Focus on automation: Automating repetitive scheduling tasks can save time, reduce human errors, and improve overall efficiency.
- Scale as necessary: Start with basic features and add complexity over time as the need for more advanced scheduling capabilities grows.
Cost Considerations in Machine Scheduling Systems
- Initial Software Costs: The upfront investment in scheduling software can vary significantly. Choosing a solution that provides essential features without unnecessary add-ons can save costs.
- Training and Support: Allocate resources for training employees on the new system. A smooth transition can avoid long-term inefficiencies and errors.
- Maintenance and Upgrades: Regular updates and maintenance help the system stay efficient, but companies must ensure that the costs for these services are reasonable.
“Selecting a scheduling software that integrates well with existing systems, automates key tasks, and scales with the company’s growth is crucial to cost-effective implementation.”
Table: Comparison of Machine Scheduling Software Features
Feature | Basic Scheduling | Advanced Scheduling |
---|---|---|
Real-Time Machine Monitoring | ✔ | ✔ |
Automated Task Allocation | ✘ | ✔ |
Integration with ERP Systems | ✔ | ✔ |
Cost Tracking | ✘ | ✔ |