Lesson 6 Dc Generators and Motors
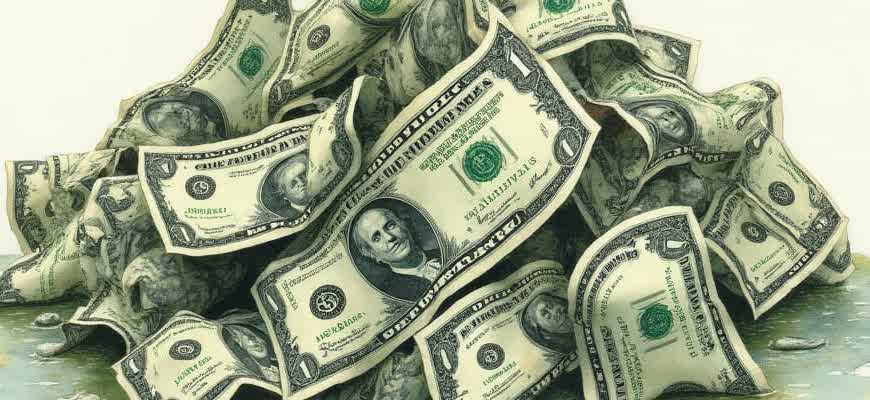
DC machines play a crucial role in electrical systems, functioning either as generators or motors depending on their application. These devices convert mechanical energy to electrical energy and vice versa, relying on the principle of electromagnetic induction. In this lesson, we will explore the construction, working principle, and types of DC generators and motors, as well as their key differences.
Key Components of DC Machines:
- Stator: The stationary part of the machine, which provides a magnetic field.
- Rotor (Armature): The rotating part that interacts with the magnetic field to produce or consume power.
- Commutator: A mechanical switch that reverses the current direction in the rotor to ensure continuous rotation or current flow.
- Brushes: Conductive elements that maintain electrical contact with the commutator.
Types of DC Generators:
- Series Generator: In this configuration, the field windings are connected in series with the armature.
- Shunt Generator: The field windings are connected in parallel with the armature, providing a constant voltage output.
- Compound Generator: A combination of series and shunt windings, offering both advantages of voltage regulation and high current output.
Important: DC motors can operate in reverse if the direction of current flow is reversed, which is achieved by changing the polarity of the power supply or by altering the commutator connections.
Difference Between DC Motors and DC Generators:
Feature | DC Motor | DC Generator |
---|---|---|
Function | Converts electrical energy into mechanical energy | Converts mechanical energy into electrical energy |
Application | Used in various devices such as fans, pumps, and electric vehicles | Used for power generation in small to medium-sized systems |
Working Principle | Electromagnetic force causes rotation of the armature | Movement of the armature within the magnetic field generates electrical current |
Lesson 6: DC Generators and Motors
DC generators and motors are fundamental devices in electrical engineering that convert mechanical energy into electrical energy and vice versa. The principles behind their operation are based on electromagnetic induction, where a conductor moving through a magnetic field generates electricity. These devices are essential in a wide range of applications, from power generation to electric vehicles.
In this lesson, we explore the working principles of both DC generators and motors, their construction, and the different types of motors and generators used in practical applications. The key difference between the two lies in their energy conversion process: while generators convert mechanical energy to electrical, motors convert electrical energy to mechanical energy.
DC Generators
DC generators operate on the principle of electromagnetic induction, where a coil of wire is rotated within a magnetic field, generating a direct current. The main components of a DC generator include the armature, field windings, commutator, and brushes. These parts work together to produce a stable output of DC voltage.
- Armature: The rotating part that generates electricity.
- Commutator: A mechanical rectifier that ensures the current flows in one direction.
- Brushes: Conductive materials that maintain electrical contact with the commutator.
DC Motors
A DC motor operates by supplying a current to a coil placed in a magnetic field. The interaction between the magnetic field and the current creates a torque, causing the coil to rotate. This rotation is harnessed to perform mechanical work. The direction of rotation is determined by the direction of the current and the magnetic field.
- Field Windings: Produce a magnetic field when current passes through them.
- Armature: A coil of wire that rotates within the magnetic field to produce torque.
- Commutator: Reverses the direction of current to maintain continuous rotation.
Key Differences Between DC Generators and Motors
DC Generator | DC Motor |
---|---|
Converts mechanical energy into electrical energy | Converts electrical energy into mechanical energy |
Generates direct current (DC) output | Requires DC input to produce rotation |
Used in power generation | Used in applications requiring motion |
Important: DC motors can be used in both variable speed and constant speed applications, depending on how the field and armature currents are controlled.
How DC Generators Work: Key Principles and Components
DC generators operate based on the principle of electromagnetic induction, where mechanical energy is converted into electrical energy. This process occurs when a conductor moves through a magnetic field, generating a flow of current. The efficiency of a DC generator depends on several key components that work together to produce steady electrical output.
In a DC generator, the basic function involves the rotation of an armature within a magnetic field. As the armature rotates, the magnetic flux cuts through the armature windings, inducing a voltage. The commutator then converts the alternating current (AC) induced in the armature into direct current (DC) suitable for practical use.
Key Components of a DC Generator
- Armature: The rotating part that generates current when exposed to a magnetic field.
- Field Windings: Create a magnetic field through which the armature moves.
- Commutator: A device that reverses the direction of current flow, ensuring the output remains in one direction (DC).
- Brushes: Maintain electrical contact with the commutator to transfer current from the armature to the external circuit.
- Shaft: The mechanical component that transfers energy to rotate the armature.
Principles Behind Operation
- The armature rotates within the magnetic field generated by the field windings.
- This motion induces an alternating current in the armature windings.
- The commutator reverses the polarity of the current, converting it to direct current.
- The brushes allow the current to flow from the armature to the external circuit.
Important: The commutator is crucial in ensuring that the current remains unidirectional, which is why the generator produces DC instead of AC.
Efficiency Factors
Factor | Impact on Efficiency |
---|---|
Armature Design | Better design leads to increased voltage output and efficiency. |
Field Strength | A stronger magnetic field improves the induction of voltage in the armature. |
Commutator Condition | Well-maintained commutators ensure smoother operation and reduce energy loss. |
Choosing the Right DC Motor for Your Application
When selecting a DC motor for a specific task, it's crucial to consider a range of factors to ensure optimal performance and efficiency. The motor type and specifications should align with the demands of the system it will power, such as load, speed requirements, and operational environment. Understanding these parameters can help avoid costly mistakes, ensuring longevity and reliability in the motor’s performance.
DC motors come in various forms, each suited for different applications. These include permanent magnet (PM), series wound, shunt wound, and compound motors. The motor choice is influenced by the desired speed control, torque characteristics, and the overall power delivery required by the system. Below are some key considerations when selecting a DC motor:
Key Factors to Consider
- Speed Requirements: Determine the motor's necessary speed range. For high-speed applications, a series-wound motor might be appropriate, while shunt-wound motors are more suitable for applications requiring consistent speed.
- Torque and Load: Assess the torque required by the application. For heavy loads, a motor capable of delivering higher torque at lower speeds may be necessary.
- Voltage and Power Supply: Ensure the motor operates within the voltage limits of your power supply to avoid overloading or damaging the motor.
- Environmental Conditions: Consider the operating environment, such as temperature, humidity, and exposure to dust or chemicals. This will influence the motor's durability and choice of casing.
Motor Types Overview
Motor Type | Key Features | Applications |
---|---|---|
Permanent Magnet Motor | Compact, cost-effective, good speed regulation | Small appliances, toys, tools |
Series Wound Motor | High starting torque, variable speed | Power tools, elevators |
Shunt Wound Motor | Stable speed, moderate torque | Fans, blowers, conveyors |
Compound Motor | Combines features of series and shunt motors, versatile | Heavy machinery, industrial applications |
Important: Always verify the motor's torque-speed curve to ensure it fits within the desired operational range for your application.
Common Troubleshooting Techniques for DC Generators
When working with DC generators, understanding the potential issues and how to resolve them is crucial for efficient operation. Common problems can arise due to mechanical failures, electrical issues, or external factors such as load conditions. Knowing how to diagnose and repair these problems can significantly reduce downtime and improve performance.
Effective troubleshooting begins with a methodical approach, which involves identifying symptoms, isolating faulty components, and performing the necessary repairs or adjustments. Below are some common techniques used to troubleshoot issues in DC generators.
1. Check for No Output Voltage
If the generator is not producing any voltage, first confirm that the field windings are properly energized. A lack of excitation current may be the cause of no output voltage. Additionally, inspect the commutator and brushes for wear or damage, as these can disrupt the electrical output.
- Ensure the field windings are not open or short-circuited.
- Verify the condition of the brushes and commutator.
- Check for proper alignment of the generator components.
2. Voltage Fluctuations
Voltage instability can occur due to fluctuating current or load conditions. Check for load imbalances, poor connections, or incorrect regulator settings. The following steps can help pinpoint the issue:
- Inspect the voltage regulator settings for proper configuration.
- Look for loose or corroded electrical connections.
- Examine the load for sudden variations or surges.
Important: Voltage fluctuations can also result from a faulty voltage regulator or improper load handling. Be sure to adjust the regulator to the generator’s rated output.
3. Mechanical Issues
Mechanical problems such as bearing failure or misalignment of the rotor can affect the overall performance of the DC generator. Regular maintenance is required to prevent these issues from becoming significant problems.
- Check the condition of bearings and replace them if worn.
- Ensure proper alignment of the rotor and stator.
- Lubricate all moving parts as required.
4. Short Circuit in the Armature
A short circuit in the armature can lead to overheating and reduced output. To diagnose this issue, conduct a resistance check and inspect the armature windings for any signs of damage or wear.
Symptom | Possible Cause | Solution |
---|---|---|
Overheating | Short circuit in armature windings | Check armature winding for shorts, and replace damaged sections. |
Low Voltage Output | Damaged armature windings | Inspect for faults and rewind armature if necessary. |
Note: Performing regular testing of armature resistance can help detect early signs of short circuits before they become a major issue.
Optimizing the Performance of DC Motors in Industrial Settings
DC motors are integral components in various industrial applications, where precision, efficiency, and reliability are critical. To maximize their performance, careful attention must be paid to several key factors including motor selection, maintenance, and operational conditions. Implementing optimization strategies ensures the motors perform at their best, reducing downtime and operational costs.
In industrial settings, maintaining peak performance of DC motors involves both understanding their technical specifications and adjusting operational practices accordingly. Several strategies can help in improving their efficiency and lifespan, while minimizing the risk of failure.
Key Factors for Optimizing DC Motor Performance
- Load Matching: Ensure the motor is properly sized to handle the load. An underloaded motor operates inefficiently, while an overloaded one may lead to overheating and premature failure.
- Cooling Systems: Adequate cooling mechanisms, such as forced air or liquid cooling, are essential for preventing overheating and ensuring consistent motor performance.
- Regular Maintenance: Routine checks for wear and tear on components like brushes, commutators, and bearings can prevent unexpected downtime.
- Speed Control: Implementing variable speed drives (VSDs) helps adjust motor speed according to load changes, which increases overall energy efficiency.
Steps for Enhancing DC Motor Efficiency
- Monitor and Adjust Motor Load: Regularly assess the load on the motor to ensure it stays within optimal operating limits.
- Minimize Power Losses: Use high-quality, low-resistance materials in motor windings to reduce energy losses.
- Implement Soft Start Systems: These systems reduce the inrush current during motor startup, preventing excessive wear and tear.
- Optimize Power Supply: Ensure that the motor receives stable, high-quality electrical input to avoid inefficiencies caused by voltage fluctuations.
"Proper maintenance and regular performance analysis of DC motors can significantly extend their operational life while enhancing efficiency, resulting in reduced energy costs and minimized downtime."
Comparison of Motor Cooling Techniques
Cooling Method | Advantages | Disadvantages |
---|---|---|
Air Cooling | Simple, cost-effective, easy to implement. | Less efficient in high-power motors, limited cooling capacity. |
Liquid Cooling | More efficient, better heat dissipation for high-power motors. | More complex and expensive to implement, requires maintenance. |
Understanding the Role of Brushes in DC Motor Efficiency
In a DC motor, brushes play a critical role in maintaining electrical contact between the rotating armature and the stationary external circuit. These components, typically made of carbon or graphite, are crucial for the conversion of electrical energy into mechanical motion. The efficiency of the motor heavily depends on the performance of the brushes and their interaction with the commutator. Proper brush design and maintenance can significantly influence the power output and longevity of the motor.
The primary function of the brushes is to ensure smooth current transfer from the external circuit to the armature windings. They press against the commutator, which, in turn, distributes electrical energy to the armature's coils. However, the friction between the brushes and commutator generates heat and wear, which can lead to energy losses and reduced motor efficiency over time. Therefore, understanding the factors affecting brush performance is essential for optimizing motor operation.
Key Factors Impacting Brush Efficiency
- Material Composition: The choice of materials such as copper, graphite, or metal-based composites influences the brush's wear rate, electrical conductivity, and heat resistance.
- Brush Pressure: Excessive pressure can increase friction, leading to more wear and less efficient power transfer. Insufficient pressure, however, can result in poor electrical contact and unstable performance.
- Commutator Condition: A smooth and clean commutator is essential for reducing wear on the brushes and ensuring efficient energy transfer.
Brush Maintenance and Its Impact on Motor Performance
Regular maintenance of the brushes, including cleaning and proper adjustment, is necessary to preserve the motor's efficiency. Failure to maintain the brushes can lead to excessive wear, electrical noise, and overheating, all of which can degrade motor performance.
Comparison of Brush Materials
Material | Advantages | Disadvantages |
---|---|---|
Graphite | Good electrical conductivity, low wear | Can produce more dust and friction |
Metal-Graphite Composite | Higher wear resistance, better for high-speed motors | Higher cost, can be brittle under extreme conditions |
Silver | Best conductivity, low wear | High cost, not suitable for all motor types |
How to Safely Maintain and Repair DC Motors
Maintaining and repairing DC motors require a systematic approach to ensure their longevity and optimal performance. Regular maintenance includes checking the mechanical and electrical components to avoid failures. Improper handling or ignoring maintenance guidelines can lead to significant damage or motor breakdowns. Understanding the motor's components and their function is key to performing safe repairs.
Before performing any maintenance, always disconnect the motor from its power source. It's essential to follow proper procedures to ensure both safety and effectiveness. Here are some key steps and precautions when maintaining or repairing a DC motor:
General Maintenance Guidelines
- Inspection of Brushes: Regularly check the condition of the brushes, ensuring they are not worn out or damaged. Replace them if necessary.
- Commutator Cleaning: Dirt and debris can build up on the commutator, affecting performance. Clean it periodically with a soft brush or cloth.
- Bearings and Shaft Inspection: Regularly inspect bearings for wear and ensure the shaft is not misaligned. Lubricate bearings to reduce friction and prevent overheating.
Repair Process
- Safety First: Always power down the motor before starting repairs. Use appropriate personal protective equipment (PPE) such as gloves and safety glasses.
- Identify the Fault: Use a multimeter to check for issues with the motor's electrical components, such as open windings or short circuits.
- Component Replacement: If a part is faulty (e.g., worn-out brushes, damaged windings), replace it with a new, compatible part.
Important: When repairing, always ensure to use parts that are specifically designed for your motor model to maintain safety and efficiency.
Key Factors in Repairing DC Motors
Component | Inspection Checklist |
---|---|
Brushes | Check for wear, damage, and proper contact with the commutator. |
Commutator | Look for cracks, dirt, or excessive wear that may cause arcing. |
Windings | Ensure there are no short circuits or open windings affecting the motor's operation. |
Comparing DC Generators with Other Types of Electrical Generators
DC generators are widely used in applications requiring direct current, but they differ significantly from other types of electrical generators. The primary distinction lies in the method of power generation and the type of output. DC generators produce a unidirectional current, whereas alternatives like AC generators (alternators) generate alternating current. Each type of generator has its advantages and specific uses based on the electrical requirements of a given system.
When comparing DC generators to other types, it is important to consider the technical aspects such as construction, efficiency, and suitability for different applications. Below is a breakdown of how DC generators compare with AC generators and other types.
Key Differences between DC Generators and Other Generators
- Current Type: DC generators provide direct current, while AC generators produce alternating current.
- Applications: DC generators are used in small-scale power systems, battery charging, and in specific industrial processes, whereas AC generators are preferred for large-scale power generation and distribution.
- Design and Maintenance: DC generators require commutators for current rectification, which increases wear and maintenance needs compared to AC generators that use slip rings.
Comparison of Generator Types
Generator Type | Output | Applications | Advantages |
---|---|---|---|
DC Generator | Direct Current | Battery charging, small electrical systems | Simple design, stable output |
AC Generator | Alternating Current | Power plants, industrial systems | Efficient for large-scale power generation |
Universal Generator | Both AC and DC | Hybrid systems, flexible applications | Versatile, adaptable to different needs |
Note: While DC generators are efficient for smaller applications, AC generators are generally more efficient in power generation for large-scale electrical grids due to their ability to transmit power over long distances with minimal loss.
The Influence of Load Changes on DC Motor Performance
Changes in the load connected to a DC motor have a direct influence on its operation, performance, and efficiency. When the load increases, the motor must work harder to maintain the required speed. This leads to changes in current, voltage, and mechanical output. The motor's characteristics, such as speed regulation and torque output, will vary depending on the load's nature and the motor’s design. Understanding these variations is crucial for optimizing motor performance in practical applications.
As the load on the motor fluctuates, several factors come into play that affect its overall functionality. The motor's response to these load changes can be better understood by analyzing the impact on the current, voltage, and efficiency. Below are some of the primary effects of load variation on DC motor operation:
Key Effects of Load Variations
- Speed Variation: With an increase in load, the motor tends to slow down unless the supply voltage is adjusted.
- Current Draw: A heavier load requires more current to maintain the desired speed, potentially leading to overheating or inefficiency if not managed properly.
- Torque Changes: The torque produced by the motor is directly proportional to the load. A higher load demands greater torque for consistent operation.
Operational Challenges with Load Changes
- Overload Protection: DC motors with insufficient protection mechanisms may overheat or suffer damage due to excessive load conditions.
- Efficiency Loss: Under varying loads, the motor's efficiency may decrease as more power is required to overcome friction and other resistances.
- Load Dependency: For motors used in precision applications, load variations can lead to fluctuations in performance, affecting accuracy and consistency.
Effective load management and understanding motor characteristics are essential for extending the lifespan and improving the performance of DC motors in industrial applications.
Impact of Load on Motor Parameters
Parameter | Effect of Increased Load |
---|---|
Speed | Decreases unless voltage is increased |
Current | Increases as more power is required |
Torque | Increases in response to higher load |