Viair Tech Support
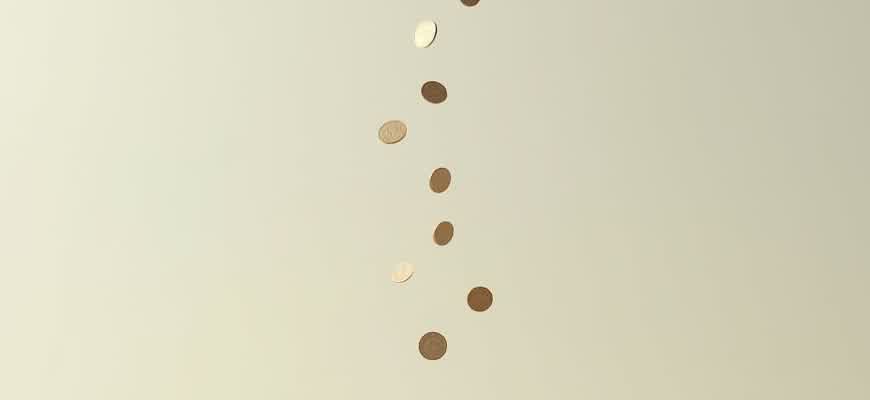
Viair offers specialized customer support to assist with various product-related inquiries and technical challenges. Their team is well-equipped to handle troubleshooting, installation guidance, and general queries regarding air compressors, pressure regulators, and other components of their product line.
Support Options Available:
- Phone Support: Speak directly with a technician for immediate assistance.
- Email Support: Submit inquiries and receive detailed responses.
- Live Chat: Real-time support through Viair's online portal.
- FAQ Section: A comprehensive list of common questions and solutions.
Common Issues Handled:
- Product installation and setup assistance.
- Troubleshooting compressor performance issues.
- Replacement parts and warranty inquiries.
For urgent technical support, Viair recommends contacting their customer service hotline directly to expedite resolution.
Support Availability:
Day | Support Hours |
---|---|
Monday - Friday | 8:00 AM - 5:00 PM (PST) |
Saturday | 10:00 AM - 2:00 PM (PST) |
Sunday | Closed |
Troubleshooting Common Problems with Viair Compressors and Accessories
If you're encountering issues with your Viair compressor or air accessories, it’s essential to understand the most frequent problems and how to address them. By performing a few basic checks, many of these issues can be resolved quickly without needing to contact technical support. Below is a guide on how to identify and troubleshoot common concerns that users experience with Viair products.
From loss of air pressure to electrical malfunctions, these issues can stem from a variety of sources. Use this guide to help diagnose and fix the problem before deciding to replace components or seek professional assistance.
Identifying and Solving Common Issues
- Low or No Air Pressure
- Check for leaks in the system. Inspect air hoses, fittings, and connections for signs of damage or wear.
- Ensure the compressor is properly sealed. Verify that the air intake valve is not clogged or obstructed.
- Verify that the compressor's duty cycle is not exceeded. If it's running continuously, it could be overheating, which might lead to low pressure.
- Compressor Fails to Start
- Confirm the power supply to the compressor. Check for blown fuses or tripped circuit breakers.
- Ensure the power switch is functional. A faulty switch may prevent the unit from activating.
- Inspect the electrical connections for any signs of corrosion or loose wires.
- Excessive Noise or Vibration
- Ensure the compressor is mounted securely on a level surface.
- Inspect for foreign objects or debris around the motor or compressor housing.
- Check that the compressor's internal components, such as the piston or cylinder, are not damaged or worn.
Important: Regular maintenance is key to avoiding most common issues with Viair products. Always inspect your compressor after heavy use and replace worn parts as needed.
Quick Check Table
Issue | Possible Cause | Solution |
---|---|---|
No Air Pressure | Leaks or clogged intake | Check for leaks and ensure intake valve is clear |
Compressor Won’t Start | Power supply issues | Inspect fuses, circuit breakers, and wiring |
Excessive Noise | Loose or worn components | Secure the unit and check internal parts for damage |
Understanding Warranty Coverage and Support for Viair Products
When purchasing Viair products, customers are assured of a solid warranty plan that covers potential defects and performance issues. However, it is essential to understand the specifics of the warranty coverage and the process for receiving technical support in case of issues. Knowing these details will help you navigate any challenges effectively and ensure that your product remains operational for years to come.
The warranty coverage for Viair products can vary depending on the specific type of item and the conditions of use. Below is a general overview of what is included and what might not be covered under warranty, as well as how to access technical support when needed.
Warranty Terms and Conditions
- Limited Warranty: Most Viair products come with a limited warranty that typically lasts between 1 to 5 years, depending on the product category.
- Coverage: Warranty generally covers defects in materials or workmanship under normal use. It does not cover damages caused by misuse, improper installation, or modifications.
- Exclusions: Items such as wear parts (e.g., valves, hoses) and damage from external factors like water or fire are usually not covered.
How to Access Viair Technical Support
- Contact Viair Support: Reach out to Viair's customer support through their official website or by phone to explain the issue you're experiencing.
- Provide Details: Be ready to provide the product’s serial number, purchase information, and a detailed description of the issue. This will help the support team assess the situation quickly.
- Return Process: If the product needs to be returned or repaired, Viair will guide you through the return process, including any shipping instructions and return forms.
Important: Always retain your original purchase receipt, as it will be required for warranty claims. Ensure that the product is properly maintained according to the manufacturer’s guidelines to prevent voiding the warranty.
Warranty Coverage Table
Product Type | Warranty Duration | Coverage |
---|---|---|
Air Compressors | 2-5 years | Defects in material/workmanship, under normal use |
Inflation Kits | 1 year | Defects in material/workmanship, under normal use |
Air Accessories | 1 year | Defects in material/workmanship, under normal use |
Using Viair's Online Resources for Quick Solutions
Viair offers a variety of online tools and resources designed to help customers troubleshoot issues efficiently. Their official website is a key starting point for finding solutions to common problems, obtaining technical support, and exploring product manuals. Whether you need step-by-step guidance or a quick FAQ response, these resources can save time and effort.
Here are some of the main ways to utilize Viair’s online support tools for rapid issue resolution:
Step-by-Step Troubleshooting
To quickly address issues with Viair products, you can follow the troubleshooting sections available on their website. These guides provide detailed instructions on how to diagnose and fix problems with your Viair equipment.
- Go to the Support section of Viair's website.
- Select the product category that matches your issue.
- Follow the instructions outlined in the troubleshooting guide for your specific product.
Online Manuals and Documentation
Viair provides downloadable product manuals and technical documentation that can be invaluable for resolving issues. These documents include everything from setup instructions to common problem resolutions.
- Visit the Manuals page on the Viair website.
- Choose your product model from the list.
- Download the PDF manual and search for relevant sections related to your issue.
Contact Viair Tech Support Directly
If troubleshooting does not resolve the issue, Viair’s online support form is an easy way to get in touch with their technical support team.
Resource | Action |
---|---|
Online Contact Form | Fill out your details and describe your problem to receive personalized support. |
Phone Support | Call the support number listed for real-time assistance. |
For immediate help, it’s always recommended to have your product's serial number and model information ready when contacting support.
What to Do When Viair Products Fail to Start or Function Properly
Viair compressors and accessories are designed for high performance, but like any equipment, they can occasionally encounter issues. If your Viair product fails to start or function properly, it is important to follow a structured approach to identify and resolve the problem quickly.
The first step is to ensure that the product is receiving power and that all connections are intact. If the unit is connected to a vehicle, check for any blown fuses or faulty wiring. Next, evaluate the product’s condition and troubleshoot potential causes like air leaks, insufficient airflow, or internal mechanical failures. Below are steps to help guide the troubleshooting process.
Basic Troubleshooting Steps
- Verify Power Supply: Ensure the power source is functioning. Check fuses, connectors, and any power switches.
- Inspect the Wiring: Look for any damaged or loose connections that could prevent proper operation.
- Check for Air Leaks: Inspect hoses, fittings, and seals to ensure there are no air leaks affecting performance.
- Evaluate Pressure Settings: Confirm that the pressure settings are adjusted correctly and match the requirements for your system.
- Test the Pressure Switch: Ensure the pressure switch is operational and not stuck in an open or closed position.
When to Seek Professional Help
If basic troubleshooting does not resolve the issue, there may be an internal fault with the unit that requires professional assistance. For example, motor failure or compressor damage may not be easily repaired without expert knowledge.
If the unit is still under warranty, consider contacting Viair’s customer support team for guidance and potential repair or replacement options.
Common Causes of Failure
Cause | Possible Solution |
---|---|
Power Issues | Check battery voltage, fuse, and power cables. Replace faulty components. |
Mechanical Problems | Disassemble the unit carefully to check for internal blockages or damage. Consult a technician if needed. |
Air Leaks | Inspect all connections, hoses, and seals for damage or wear. Replace any faulty parts. |
Preparing Your Viair Equipment for Long-Term Use: Tech Support Insights
Maintaining your Viair equipment for optimal performance over extended periods is essential for avoiding unexpected breakdowns. Whether you're storing your compressor for the off-season or ensuring it’s ready for heavy-duty use, proper preparation is key to longevity. Here are some crucial tips based on the guidance from Viair's tech support team that will help you protect your gear and maximize its lifespan.
Following these steps before storing or regularly using your Viair system ensures the longevity and reliable performance of your compressor. Let’s dive into essential maintenance routines and storage techniques.
Key Maintenance Tips for Viair Equipment
- Check and Replace Air Filters: Ensure your air filter is clean or replaced before storing the compressor for long periods. Clogged filters can hinder airflow, reducing performance.
- Inspect for Leaks: Regularly check for leaks in air lines and connections. Even small leaks can lead to reduced efficiency and unnecessary strain on your system.
- Lubrication: Apply lubricant to moving parts like the piston and motor shaft, especially if the compressor has been in storage for an extended period.
Storage Recommendations
- Keep the Unit Dry: Store your equipment in a dry, cool environment to prevent rust or corrosion, especially if the equipment is metal-based.
- Avoid Extreme Temperatures: Exposure to extreme heat or cold can damage the motor or other components. Keep the compressor in a temperature-controlled area.
- Disconnect Battery: If your unit has a battery, disconnect it before long-term storage to prevent discharge or damage.
Important: Before resuming use after storage, always perform a system check to ensure everything is in working order, and check the battery voltage if applicable.
Key Components to Monitor
Component | Maintenance Task |
---|---|
Compressor Motor | Lubricate motor parts, check for any loose components, and ensure there are no obstructions. |
Pressure Switch | Inspect for functionality, ensure that it is securely mounted, and clean the contacts if necessary. |
Air Tank | Check for signs of corrosion, clean the tank, and make sure it is tightly sealed. |
By following these tips and staying proactive with maintenance, you’ll keep your Viair equipment running smoothly for years to come. A little preparation goes a long way in preserving its performance and functionality.
How to Fix Leaks and Pressure Problems in Air Compressors
Air compressor leaks and pressure issues can significantly affect performance and efficiency. These problems often arise from improper sealing, damaged components, or wear and tear over time. Identifying the source of the issue is key to resolving it. The following steps will guide you through troubleshooting and repairing common leaks and pressure problems in your air compressor.
Before you begin any repairs, ensure that the system is turned off and disconnected from power to prevent injury. Once you have a safe working environment, you can start by checking the key components that are most likely to be the source of the issue. Below are some typical steps to follow when diagnosing and fixing air compressor leaks and pressure issues.
Steps to Resolve Air Compressor Leaks
- Inspect the Air Hoses: Examine all hoses for cracks, abrasions, or other signs of wear. Replace any damaged hoses immediately.
- Check for Loose Connections: Ensure that all fittings and connections are tight. Use a wrench to tighten any loose components, but avoid over-tightening, which can cause damage.
- Examine the Valve Seals: Leaking seals in the pressure valve or check valve can lead to air loss. If you find any worn seals, replace them as needed.
- Look for Rust or Corrosion: Rust or corrosion on the compressor components can compromise their integrity. Clean any corroded areas and apply protective coatings to prevent future damage.
How to Address Low Pressure Issues
- Check the Pressure Regulator: The regulator controls the output pressure. If it's malfunctioning, adjust or replace it to restore proper pressure levels.
- Examine the Intake Filter: A clogged intake filter can restrict airflow, causing low pressure. Clean or replace the filter to ensure optimal airflow.
- Inspect the Compression Mechanism: If the piston or diaphragm is worn out, it can lead to insufficient pressure. In this case, you may need to replace these parts to restore full functionality.
Important: Always verify that the air compressor is operating at the manufacturer’s recommended pressure range to avoid overloading the system or causing further damage.
Common Causes of Air Leaks and Pressure Loss
Component | Potential Issue | Recommended Solution |
---|---|---|
Air Hoses | Cracks or damage | Replace damaged hoses |
Pressure Valve | Worn seals | Replace valve seals |
Regulator | Malfunctioning | Adjust or replace the regulator |
Advanced Troubleshooting: Fixing Electrical Problems in Viair Systems
Electrical issues in Viair systems can stem from various causes, and identifying the root cause requires systematic checks and troubleshooting. The following guide covers key steps to address common electrical problems that can affect the functionality of air compressors and other Viair devices.
Before diving into more complex repairs, ensure that you’ve checked basic elements such as power sources and fuses. For more persistent issues, deeper diagnostics and repairs are necessary, such as inspecting wiring, connectors, and control modules. Below is a structured approach to resolving electrical problems efficiently.
Steps for Diagnosing Electrical Failures
- Power Supply Check: Ensure the power source is functioning and providing the required voltage. A multimeter can help confirm the voltage consistency.
- Inspecting Fuses: Fuses are a common point of failure in electrical systems. Check for blown fuses and replace them as needed.
- Wiring Inspection: Look for frayed wires or loose connections. Pay special attention to high-stress areas such as where wires are bent or exposed to heat.
- Connector Verification: Ensure all connectors are clean and secure. Dirty or corroded connectors can result in poor electrical conductivity.
- Control Module Testing: Test the control module for any faults using diagnostic tools or multimeter readings. Faulty modules may require replacement.
Common Issues and Fixes
- Compressor Not Turning On:
- Check the battery voltage and connections.
- Ensure the fuse is not blown.
- Test the pressure switch and replace if faulty.
- Inconsistent Power Supply:
- Verify the wiring for loose or damaged connections.
- Inspect the relay for proper function.
- Check for corrosion in the power circuit.
- Blown Fuse Issues:
- Check the system for short circuits.
- Replace the fuse with the correct amperage rating.
- Inspect the compressor’s motor for damage or wear.
Quick Reference Table: Troubleshooting Electrical Issues
Issue | Solution |
---|---|
Compressor Won't Start | Check for battery power, verify fuse condition, test pressure switch. |
Low Voltage | Inspect wiring and connections, replace faulty relay, check alternator output. |
Frequent Fuse Blowouts | Look for short circuits, replace with proper fuse, inspect compressor motor. |
Note: Always ensure that the power is turned off before performing any repairs or maintenance to avoid electrical shock or further damage to the system.